All published articles of this journal are available on ScienceDirect.
The Effect of Surface Roughness on Repair Bond Strength of Light-Curing Composite Resin to Polymer Composite Substrate
Abstract
Objective:
The purpose of this study was to analyze the shear bond strength of a new composite resin to polymer-based composite substrates using various surface roughnesses and two kinds of polymer matrices.
Materials and methods:
Particulate filler composite resin with cross-linked polymer matrix and fiber-reinforced composite with semi-interpenetrating polymer matrix were used as bonding substrates after being ground to different roughnesses. Substrates were aged in water for one week before bonding to new resin composites. Twelve specimens in the substrate groups were ground with grinding papers of four grits; 320, 800, 1200 and 2400.
Results:
Corresponding values of surface roughness (Ra) varied from 0.09 to 0.40 for the particulate filler composite resin and 0.07 to 0.96 for the fiber-reinforced composite resin. Characteristic shear bond strength between the new resin and particulate filler composite resin was highest (27.8 MPa) with the roughest surface (Weibull modulus: 2.085). Fiber-reinforced composite showed the highest bond strength (20.8 MPa) with the smoothest surface (Weibull modulus: 4.713).
Conclusions:
We concluded that surface roughness did not increase the bonding of new resin to the substrate of IPN based fiber-reinforced composite, whereas the roughness contributed to bonding the new resin to the particulate filler composite resin with a cross-linked polymer matrix.
INTRODUCTION
Repairs of old restorations are common clinical and technical procedures in dentistry. Most often these procedures are related to repairing or replacing an existing composite resin restoration. The declining use of amalgam and other metal restorations and appliances, and the increasing use of composite resin restorations have stressed the importance of the bond strength quality of light-curing composite resin to polymer based composite substrates. By repairing the old restoration intact tooth tissue can often be preserved. The repair process is usually more cost-effective than the fabrication of a new restoration. The use of polymer based devices, e.g. composite fillings of fibre-reinforced composite (FRC), fixed dental prostheses, and crowns have become more popular [1-7]. As the use of polymer based materials increases, the necessity for repairing fractured, discoloured, or worn restorations also increases. In repairs, the durable and reliable adhesive joint between the substrate and the repair composite is crucial for clinical success. Attempts to develop composite repair primers have been made, but the bonding of the new composite to the old composite substrate remains problematic [8].
The importance of the age of the polymeric substrate on the repair strength was previously evaluated by Lloyd et al. [9] and Boyer et al. [10]. These studies demonstrated that the bond strength of the composite to the fresh composite was the same as the cohesive strength of the bulk material. Söderholm and Roberts [11] compared the repair bond strength of composite after storing the repaired composite specimens in water for 3 months and 12 months. They discovered that the repaired resin had a tendency to weaken during the storage period. Özcan et al. [12] found that the composite-to-composite bond strength varied in accordance with the specific particulate filler, composite resin, and different surface conditioning methods used. Several methods for repairing polymer based fillings and appliances have been introduced. Usually the bonding procedure includes treating the substrate with adhesive resin, also called intermediate resin, and combining it with a roughened substrate surface by air-particle abrasion or grinding [13-16]. Composite repairs have bond strengths of approximately 20% to 70% of the cohesive strength of bulk materials.
In our previous study, the effect of intermediate adhesive resin treatment was evaluated with various substrates [2]. We have also studied the effect of application time of the intermediate resin on bond strength when applied to the composite [17]. Studies have shown that the intermediate resins improved the bond strength of repaired restorative composite [2, 18-20]. Several research groups have found that air-particle abrasion produces satisfactory and reproducible bond strength values, although these values are not significantly different from the results obtained with diamond bur grinding [21-23]. Laboratory studies by Crumbler et al. [21], Söderholm et al. [11], and Turner and Meiers [24, 25] have also evaluated the strength of repaired composites. These studies showed that the surface irregularity of the composite substrate had a greater influence on bond strength compared to the use of intermediate resin only. Therefore, surface roughness is an important factor in creating high repair strength in cases where repair resin has the necessary physico-chemical properties, which allows for wetting of the rough surface [23, 19]. The aim of this study was to investigate the influence of surface roughness of a particulate filler composite resin and a fiber-reinforced composite resin substrates on the repair composite.
MATERIALS AND METHODS
In this study particulate filling composite resin (Z100) was bonded to three different types of substrate. The materials used in this study are listed in Table 1. The substrates for the test specimens were prepared by placing either continuous unidirectional E-glass fiber-reinforced composite (FRC) (everStick), with light-curing semi-interpenetrating polymer network (IPN) polymer matrix, or light-curing particulate filler composite resin (Z100) with cross-linked polymer matrix into the retentive cavity of the supporting acrylic resin block. These were surrounded by a stainless steel cylinder. Both substrates of FRC and particulate filler composite resin were light polymerized with a light-curing hand-unit (Optilux-501, Kerr, CT, USA) for 40 s. The light wavelength was between 380 and 520 nm with an intensity of 720 mW/cm2. Both the light wavelength and intensity were verified by an internal radiometer, and the FRC substrate was additionally cured in the oven for 15 min in Liculite (LicuLite, Dentsply DeTrey GmbH, Dreieich, Germany). The substrates were stored at 37˚C in water for one week to age the substrate; i.e. to let the polymerization process and free radical activity complete. The aged substrate surfaces were then wet ground with 320, 800, 1200 and 2400-grit (FEPA) silicon carbide grinding paper (Table 2). 3M Multipurpose adhesive resin was applied as an intermediate resin to the surface of the substrate and left to react for 5 min in dark conditions and then light cured for 10 sec (Optilux 501). A five minute reaction time was observed to allow for the diffusion of the intermediate resin into the microirregularities and polymer structure of the substrate. Composite resin Z100 was then applied in 2 mm increments to the substrate surface using a translucent polyethylene mould with a 3.6 mm diameter. It was then polymerized with a light-curing hand-unit for 40 s.
Materials Used in this Study
Brand | Manufacturer | Lot no. | Code | Chemical composition |
---|---|---|---|---|
Z100 | 3M Dental Products, St. Paul, MN, USA | OHR | Z100 | Bis-GMA,UDMA, Bis-EMA, TEGDMA |
everStick | StickTech-GC, Turku, Finland | eS | E-glass-fibers impregnated with IPN of dimethacrylate and PMMA | |
3M Scotchbond Multipurpose Adhesive | 3M Dental products, St. Paul, MN, USA | 20011115 | MP | Bis-GMA, HEMA |
PMMA = poly(methylmethacrylate)
bisGMA = bisphenol A-glycidyl dimethacrylate
TEGDMA = Triethylene glycol dimethacrylate
UDMA = Urethane dimethacrylate
Bis-EMA = Bisphenol A polyethylene glycol diether dimethacrylate
HEMA = Hydroxyethylemethacrylate
IPN = Interpenetrating polymer network
Twelve specimens (n=12) for each material combination of substrate and Z100 stub were stored in water at 37 oC for 48 h. Shear bond testing was applied using a universal testing machine (model LRX, Lloyd Instruments, Fareham, England), and the data was recorded using PC-software (Nexygen, Lloyd Instruments Ltd., Fareham, England). The specimens were mounted into a jig (Bencor Multi-T shear assembly, Danville Engineering Inc., San Ramon, CA) and loaded with a circular shearing rod until they fractured with a crosshead speed of 1.0 mm/min. FRC eS specimens were mounted with their fibers vertically oriented, i.e. along the direction of shear force.
Profilometry (Mitutoyo Surftest 301, Japan) measured the surface roughness (average roughness, Ra) of the substrates after grinding. Fiber-reinforced composite substrate was measured in relation to the direction of the fibers; transversally and longitudinally. Three repeated roughness measurements were conducted for each substrate group.
The shear bond strength values for all groups were analysed with analysis of variance (ANOVA) using SPSS 10.0 (Statistical Package for Social Science, SPSS Inc., Chicago, Illinois, USA). Weibull analysis was carried out to calculate characteristic bind strength and Weibull modulus. The primary form of the Weibull distribution is described below:
where m = Weibull modulus (also known as a shape factor), a constant, which determines the slope of the distribution function and characterizes the spread of the failure data with respect to the σ (=strength) axis. σo =characteristic strength (i.e the stress level at which 63% of the specimens have failed) and σ u = theoretical failure stress at which the failure probability approaches zero and is known as the threshold stress (MPa). Pf is the probability of failure, which varies from 0 to 1. The correlation coefficient r was calculated from linear regression models with logarithmic transformations.
RESULTS
The average surface roughness (Ra) of composite Z100 decreased from 0.41 to 0.04 by changing the grit size of grinding papers from 320 to 2400 (Table 2). FRC eS showed higher roughness than composite Z100 after it was ground with 320 grit grinding paper (Ra = 0.91) but the difference with Z100 decreased with the use of 800 to 2400 grit grinding papers. No difference was detected in the surface roughness when the FRC eS was measured transversally or longitudinally to the direction of the fibers. A rougher surface of composite Z100 resulted in higher shear bond strength values than a smoother surface (p<0.001) (Fig. 1). Surface roughness of FRC eS with two fibre directions did not differ statistically (p>0.05). The substrate ground with 2400 grit grinding paper obtained the highest bond strength, i.e. the smoothest surface (Fig. 1). Fig. (2) presents the average shear bond strength values plotted against surface roughness. Fracture patterns by visual analysis and light microscope showed mainly adhesive failures for the Z100 substrate and cohesive failures for FRC with a debonding of individual fibers from the polymer matrix. No signs of intermediate resin existed on the surface.
Average Surface Roughness (Ra) of Substrates Being Ground with Grinding Papers of Various Grits
Substrate | Surface Roughness (Ra) | |||
---|---|---|---|---|
320 Grit | 800 Grit | 1200 Grit | 2400 grit | |
eS tranversal | 0.91 | 0.22 | 0.20 | 0.05 |
eS longitudinal | 0.85 | 0.29 | 0.20 | 0.03 |
Z100 | 0.41 | 0.21 | 0.08 | 0.04 |

Mean shear bond strength of particulate filler resin composite to substrate of composite Z100 and FRC eS which have been ground with different grit size grinding papers. Vertical lines represent standard deviations.
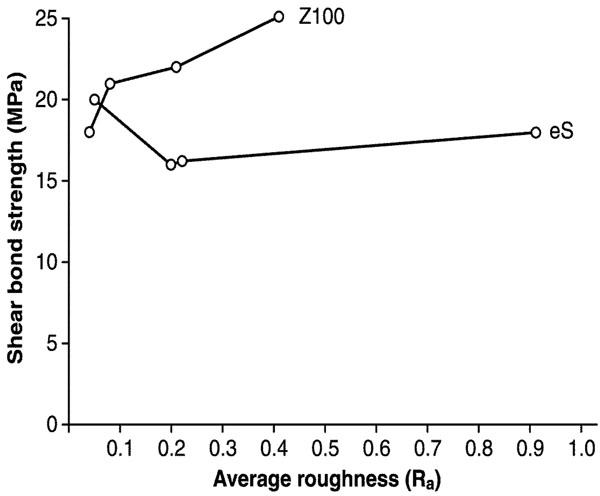
Average surface roughness (Ra) plotted against shear bond strength in MPa.
A surface roughened by 320 grit grinding paper had the highest characteristic bond strength (27.805 MPa) with composite Z100, but a roughness obtained with 800 grit grinding paper had the highest Weibull modulus (2.787) (Table 3) (Fig. (3a). With the FRC eS, the smoothest substrate surface, i.e. after it was ground with 2400 grit grinding paper, had the highest characteristic bond strength (21.652 MPa) and Weibull modulus (4.713)(Table 3)(Fig. 3b).
Results of the Weilbull Analysis
Group | Characteristic Strength = So | Weibull Modulus =m | Correlation r-Coefficient |
---|---|---|---|
eS-320 grit | 20.885 | 1.940 | 0.984 |
eS-800 grit | 18.858 | 3.357 | 0.969 |
eS-1200 grit | 18.310 | 2.420 | 0.936 |
eS-2400 grit | 21.652 | 4.713 | 0.964 |
Z100-320 grit | 27.805 | 2.085 | 0.932 |
Z100-800 grit | 24.580 | 2.787 | 0.959 |
Z100-1200 grit | 18.310 | 2.420 | 0.936 |
Z100-2400 grit | 20.752 | 2.632 | 0.973 |
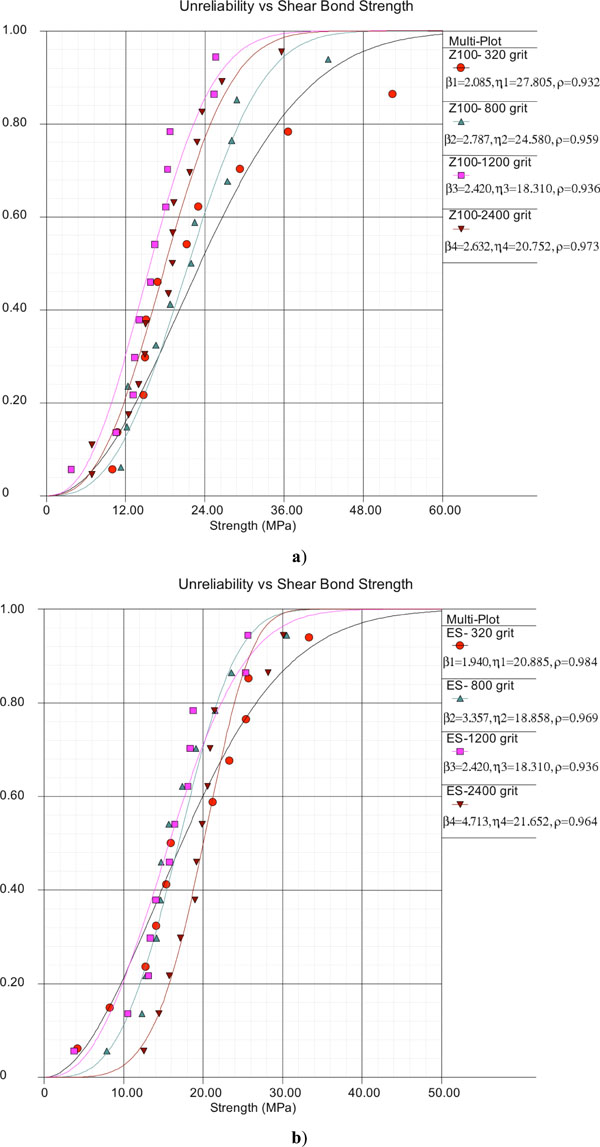
Graphs of the results of Weilbull analysis: a) composite Z100 and b) FRS eS.
DISCUSSION
Interlocking roughness could be described as an essential component of micromechanical retention in order to distinguish it from gross mechanical retention [26]. Gross retention refers to matter which prevents a restoration from falling out. It is used for amalgam and other direct restorative materials. Interlocking roughness is a smaller scale method of resisting shear or tensile forces. In this study, roughness represents micromechanical retention. Methodologically one needs to take into consideration that analysis of shear bond strength is typically combined with fracture pattern analysis of brittle materials. However, in this study, the substrate was a polymer based anisotropic FRC with a different fibre orientation for each study group. The substrate also contained an isotropic particulate filler composite. This makes statistical evaluation according to the classic Griffit´s critical defect theory [27] of brittle isotropic materials difficult. Therefore the results of the Weibull analysis can only be considered indicative. Furthermore, the fracture pattern analysis is influenced by the diffusion of intermediate resin (Multipurpose adhesive) to the polymer matrix which is slightly plasticized in nature. This means that no remnants of the polymerized intermediate resin could be found visually. It is possible that differences in the elastic modulus of the substrate could have diffused and polymerized the intermediate resin as well as bonded the particulate filler composite resin, changing the gradient of the mechanical structure from a more resilient material towards a more brittle material. This could have influenced the fracture mechanics and stress distribution.
The present study did not support the expectation that rougher surfaces would improve the shear bond strength of one composite to another composite. It was interesting that, in the case of the FRC eS substrate, a rough surface did not provide better shear bond strength. It was assumed that the rough grinding paper would create more microscopic undercuts in the FRC eS substrate matrices then the composite Z100 substrate. Composite substrate is composed of polymer matrix and exposed inorganic fillers or fibers as bonding sites for new resins. Boyer and Chan [9] found that highly filled composites exhibited the highest bond strengths. In the case of focusing on improving the bonding of resins to the surface of inorganic fillers, silane coupling agents may provide improvement for bonding. Silane function is based on the existence of hydroxyl groups on the surface of an inorganic substrate. Due to this, the use of silane function is not applicable with polymer substrates [28].
Polymer matrices of commonly used filling composite resins and the majority of brands of FRCs are based on dimethacrylates which form a highly cross-linked polymer after they are polymerized. Cross-linked polymers are difficult to swell and dissolve in order to obtain an optimal penetration of monomers of the repair resin into the polymer structure of the substrate. This complicates the bonding of old composite resins to new resins. Alternatively, existence of non cross-linked polymer phases in the polymer matrix of composites, e.g. in the form of semi-interpenetrating polymer networks (IPN), allows bonding to occur by way of substrate dissolution and the penetration of new resin into the polymer structure [29]. This study used a cross-linked matrix in composite Z100 and an IPN matrix in FRC eS. The results demonstrated better bonding to the cross-linked matrix if the surface was rough, whereas IPN matrix demonstrated better bonding with a smooth surface. This indicates that the benefits of a polymer bonding surface with an IPN structure can be utilized even with smooth bonding surfaces. Lastumäki et al. [8] determined that the intermediate resin used in their study (MP) had relatively good dissolution capacity in the linear phases of the polymer matrix of the FRC eS substrate. Before polymerization of the new resin, the monomers of the intermediate resin had already swollen the IPN containing polymer matrix of the substrate and durable bonding was established. Bond strength was not dependent on micromechanical irregularities as in the case of highly cross-linked composite substrate, due to the multiphase structure of the FRC substrate.
Earlier studies have shown that bond strength decreases when the oxygen inhibited surface layer of the substrate is removed or impaired [9, 30-32]. The possibility of obtaining free radical polymerization after the substrate surface is ground down is relatively low due to a small number of unreacted carbon-carbon double bonds on the polymer surface [8, 30]. The highest reaction between a substrate and the formation of a covalent bond occurred during the first 24 hours after polymerization of the substrate [31, 33]. In this study, the substrates were aged for one week. This is likely the explanation why the bond strength of the composite substrate was dependent on micromechanical interlocking in the case of composite Z100, whereas bonding seemed to contribute to the bonding mechanism of swelling and dissolving the IPN matrix in the case of FRC eS. It is likely that fresh composite resin substrate would have provided better bond strength.
Our study concludes that surface roughness did not improve the bonding of new resin to the substrate of IPN based fiber-reinforced composite, whereas the roughness contributed to bonding the new resin to the particulate filler composite resin with a cross-linked polymer matrix.
DECLARATION OF INTERESTS
Pekka Vallittu consults Stick Tech LTD in research and development.
CONFLICT OF INTEREST
The authors confirm that this article content has no conflicts of interest.
ACKNOWLEDGEMENTS
Declared none