All published articles of this journal are available on ScienceDirect.
Implant-supported Overdenture using CAD/CAM Milled Bar and Locator Attachments: A Technical and Case Report
1. INTRODUCTION
Completely edentulous patients with extensive residual ridge resorption often suffer from reduced chewing ability and unstable dentures. Additionally, patients with sharp bony projections or knife-edge ridges that cause pain upon occlusal loading may particularly benefit from implant-supported prostheses [1, 2].
The introduction of dental implants has significantly improved both the functional and psychological outcomes for completely edentulous patients. Implant overdentures offer several advantages, including enhanced retention and stability, preservation of surrounding bone, improved masticatory function, and increased overall patient satisfaction [3-7]. The occlusal load is shared between the mucosa and implants, reducing soft tissue abrasion and discomfort. Moreover, implant overdentures are relatively less complex than fixed implant prostheses, can improve facial esthetics through labial flanges, can be removed at night to help control nocturnal parafunctions, and require fewer implants, making them a more affordable option [1, 8, 9].
Generally, there are two mechanisms by which dental implants are used for anchorage of overdentures: solitary abutments or connected abutments using a rigid bar. Solitary abutments provide retention for the denture, while support is mainly achieved through the oral mucosa. This type of attachment is preferred for its simplicity and lower cost, but achieving abutment parallelism can be challenging when more than two implants are involved. When multiple implants are used, they are usually splinted with a rigid bar, which improves support and reduces the load on the oral mucosa. Additionally, rigid bar attachments are associated with less marginal bone loss and lower maintenance requirements compared to solitary abutments. Retentive components are commonly added to the bar in the form of clips or stud attachments (e.g., ERA or locator abutments) [8].
Several biomaterials can be used to fabricate implant-supported overdenture bars [10]. Cast gold alloys were among the earliest materials employed due to their excellent biocompatibility and corrosion resistance. However, they need to be made considerably thick to provide the required rigidity, and their use has significantly declined due to their high cost [11]. Base-metal alloys, mainly cobalt-chromium, are widely used because of their high elastic moduli, corrosion resistance, and low cost. These alloys require special casting machines due to their high melting point, and achieving completely passive seating can be challenging because of high solidification shrinkage. Nickel-based alloys may cause allergic reactions in some patients [12]. Nowadays, titanium alloys are favored for their outstanding biocompatibility, lightweight nature, good mechanical properties, and machinability [10]. Zirconia offers good mechanical properties and superior esthetics. As a ceramic, it is suitable for patients with metal sensitivities; however, its high hardness can lead to rapid wear of retentive clips, brittleness, and concerns regarding long-term durability [13, 14].
Alternatively, newly introduced high-performance polymers like PEEK (Polyetheretherketone) and BioHpp (Bio High-Performance Polymer) are known for their biocompatibility, low plaque affinity, less wear of retentive clips, and lightweight [13, 15].
There are three methods to incorporate locator abutments into an overdenture bar. The first, known as the cast-to method, involves adding the locator abutment to the wax pattern, which is then cast in high noble alloy. The second method involves directly welding the locator abutment to the finished bar using laser welding. The third method, drilling and tapping, entails drilling the finished bar, then tapping and torquing the locator abutment into place [16]. This last method ensures complete retrievability of the female locator abutment in case of wear or damage [17-19].
The objective of this clinical report is to describe a fabrication technique for a milled titanium implant overdenture bar with locator abutments using the drilling and tapping method, along with a novel technique to duplicate the master cast before denture processing.
2. CASE REPORT
2.1. Case Presentation
A 70-year-old female patient of Caucasian ethnicity presented to our clinic complaining of uncomfortable and loose dentures. Her medical history was significant for hypertension, asthma, and type II diabetes. She was under routine care from her physician. She had these dentures for several years, and her previous dentist could not help her anymore. The patient was seen multiple times in the emergency clinic, multiple denture adjustments were made, and the rubber inserts of the implant attachments were replaced, but she was still not satisfied with the retention and stability. She requested a more definitive solution
2.2. Clinical and Radiographic Examination
The patient was completely edentulous with a knife-edge ridge in the mandible (Fig. 1A-D).
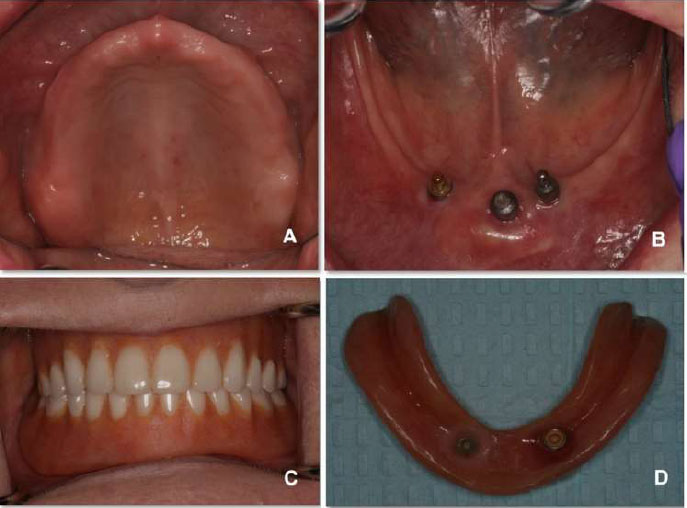
Initial presentation A) Maxillary residual ridge. B) Mandibular residual ridge with Spheroflex attachments on implants # 33 and 43, and healing abutment on #31. C) Retracted frontal view in occlusion, pre-operative D) Fitting surface of mandibular denture.
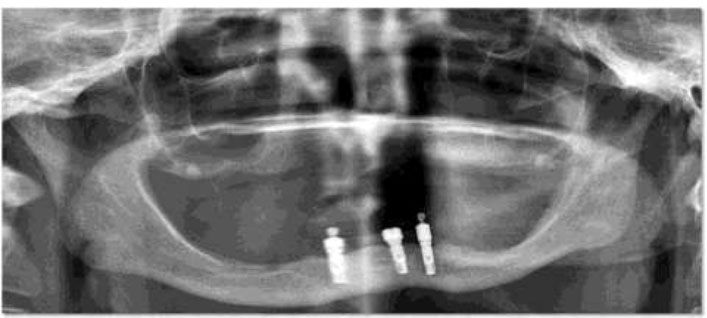
Radiographic evaluation, pre-operative panoramic X-ray.
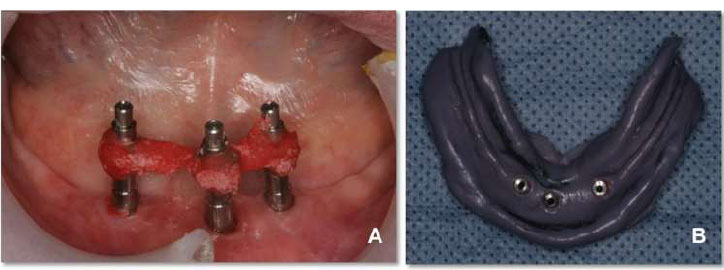
Lower master impression. A) Open-tray impression copings splinted using Duralay resin. B) PVS impression using a custom tray.
According to the Prosthodontic Diagnostic Index Classification, she was classified as class III due to mandibular bone height of 10-15 mm (Fig. 2) and temporomandibular joint disorder symptoms [14]. She had three narrow-platform (3.3 mm × 10 mm) Mark III Branemark implants (Nobel Biocare Services AG) placed in the anterior mandible, retained with two Spheroflex attachments. These implants had been functioning for more than 10 years. The Spheroflex attachment is a self-paralleling spherical abutment designed to correct up to 15° of implant divergence, facilitating easier insertion for the patient and minimizing attachment wear (Preat Corporation).
2.3. Treatment Plan and Management
Due to limited bone height and the patient’s concerns about undergoing further surgical treatment, a fixed implant prosthesis was not advocated. The proposed treatment plan involved an implant-supported lower overdenture with a milled Titanium bar and locator attachments, along with an upper conventional denture.
Open-tray impression copings were seated on each implant and splinted using inlay pattern resin (Duralay, Reliance Dental Manufacturing LLC). Definitive impressions were then made with polyvinyl siloxane addition silicone impression material (Aquasil Ultra Monophase; Dentsply Sirona) using custom trays fabricated from Triad VLC Custom Tray Material (Dentsply Sirona) (Fig. 3A-B). The impression was poured using Type IV dental stone (Silky Rock, Whip Mix Corp). Non-engaging temporary titanium abutments (Nobel Biocare Services AG) were seated on the laboratory analogues and splinted with Triad resin to fabricate a verification jig (Fig. 4A-C).
Then, the jig was sectioned using a separating disc, and each abutment was seated intraorally on its corresponding implant. Periapical radiographs were made to confirm complete seating before joining the verification jig parts together using flowable composite. The splinted verification jig was re-seated on the master cast to verify accuracy and passive fit using a one-screw test (Sheffield test) (Fig. 4A-D) [20].
Face-bow registration and centric relation record were completed, and the casts were mounted on a semi-adjustable articulator (Hanau Wide Vue, Whip Mix Corp). Teeth try-in was completed, and occlusion, esthetics, and phonetics were evaluated. The master cast and the dentures were scanned using Nobel Procera Conoscopic Scanner (Nobel Biocare USA LLC.), and the bar was designed using CAD software (Fig. 5).
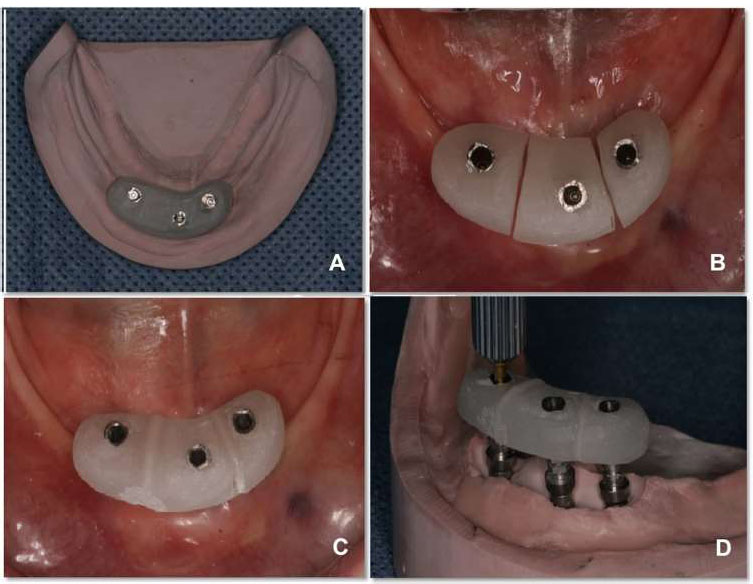
Verification jig fabrication. A) Temporary abutments on the master cast were joined using Triad resin. B) Sectioned jig seated intraorally. C) Jig joined using flowable resin. D) One-screw test is performed to ensure complete passing seating.
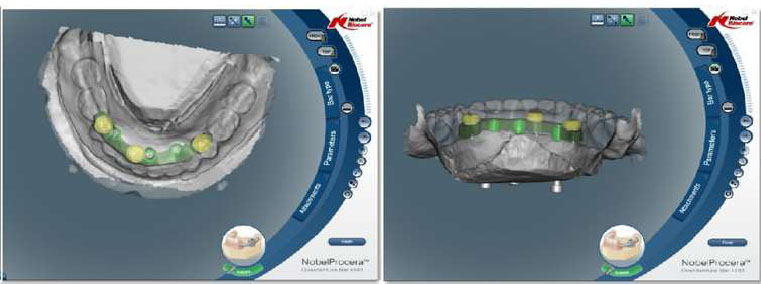
Milled bar CAD design using nobel procera.
Once the design was approved, the bar was milled in Ti-6Al-4V Titanium alloy. This alloy offers a combination of strength and biocompatibility and is known for its wide availability. Three locator abutments (Preat Corporation) were tapped and threaded into the bar. The milled bar was then tried in, and periapical radiographs were taken to verify complete passive seating (Fig. 6).
A second teeth try-in was completed with the milled bar in situ. Later, the master cast with the bar was duplicated (All-purpose duplicating material, Ticonium), and locator analogues were inserted in the duplicate mold and poured in Type III dental stone (Microstone, Whip Mix Corp) (Fig. 7A-D).
The overdenture was processed on the duplicate working cast using heat-cured acrylic resin (Lucitone 199, Dentsply Sirona). After deflasking, the working cast was intentionally broken to retrieve the overdenture. The denture was then finished and polished. At the delivery appointment, the milled bar was placed, and the screws were torqued to 35 N·cm, followed by the insertion of the overdenture. Occlusion, esthetics, and phonetics were verified, and postoperative instructions were provided (Fig. 8A-C).

Milled Titanium overdenture bar with tapped locator attachments tried in the patient mouth and periapical x-rays taken to verify complete seating.
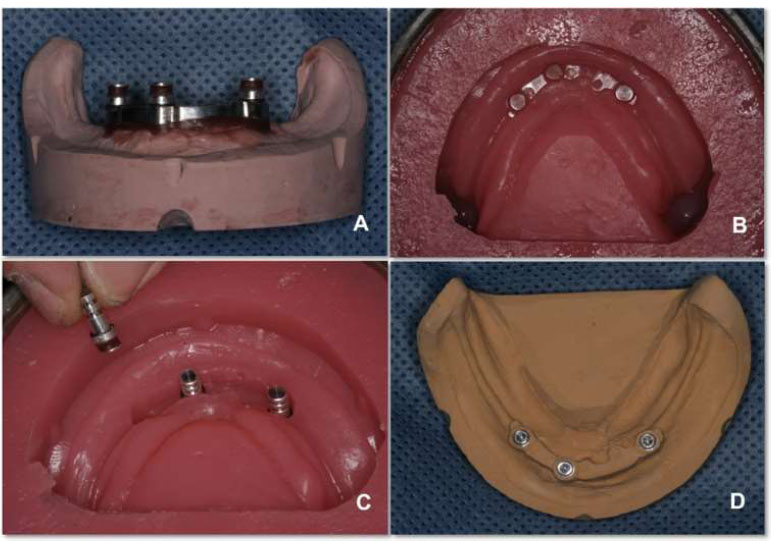
Duplication of the master cast with the overdenture bar. A) Undercut under the milled bar is blocked-out with wax and locator impression copings seated on locator abutments. B) Duplicate mold. C) Locator analogues are connected to locator impression copings and seated in the duplicate mold. D) Duplicate working cast with the locator analogues.
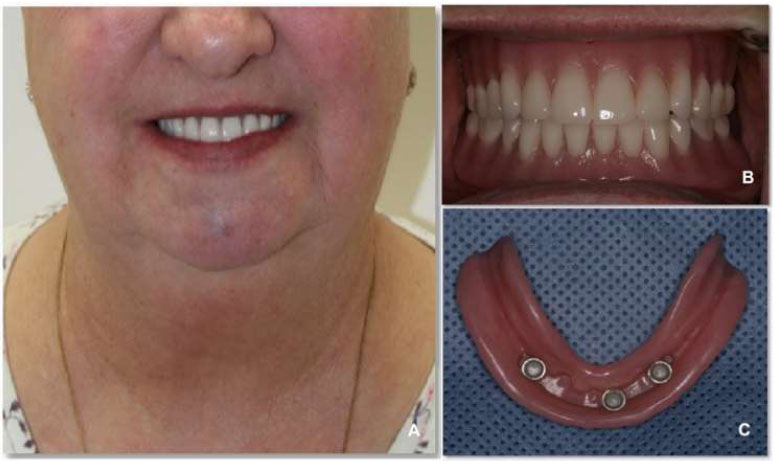
Delivery. A) Smiling view. B) Frontal retracted view in occlusion, post-operative. C) Fitting surface of mandibular overdenture with locator inserts.
One week later, a clinical remount was performed to achieve final occlusal refinement.
The patient was seen for follow-ups at 1 week, 1 month, and every 6 months thereafter, for a total of 18 months. At each visit, soft tissue health was evaluated for abrasions or signs of inflammation. Periodontal probing was performed to assess the health of the implants. The patient’s pain score and satisfaction were also evaluated. She reported significant improvements in denture stability, chewing efficiency, and self-confidence with her new prostheses. Overall, she was satisfied and comfortable with the functional and esthetic outcomes of the treatment.
3. DISCUSSION
This clinical report discusses clinical and technical steps to fabricate a complete implant-supported overdenture with a milled bar and locator attachments. The milled overdenture bar provides exceptional support to the denture, which minimizes tissue-ward movement and ultimately reduces soft tissue trauma or discomfort. Intimately fit denture base against the milled axial surfaces of the Titanium bar creates guiding planes that limit the path of insertion and significantly improve lateral stability [21, 22]. Moreover, the use of Titanium alloy reduces the weight of the bar and the cost of the treatment by eliminating the need for the more expensive noble alloy. The self-aligning locator abutments facilitate insertion and removal by the patient even in cases of limited manual dexterities, yet offer a wide range of retentive values that can be easily maintained or modified per patient request [17, 19].
Two technical points were emphasized in this report. The first is the use of tapped and threaded locator abutments, which ensures complete retrievability and facilitates maintenance if the female abutment becomes broken or worn down [17]. The second point is the use of a duplicate working cast for processing the overdenture. Direct processing of acrylic resin on the actual bar may cause the resin to lock under the milled bar, increasing the risk of overdenture fracture or damage to the bar upon retrieval. Additionally, preserving the master cast serves as a permanent record for the patient, aiding future reference and maintenance [23].
There are several limitations of implant overdenture bars that must be considered. They are more complex and require advanced training for both the dentist and the laboratory technician. Additionally, they are more costly compared to solitary abutments. Implant bars also require greater vertical space, approximately 15 mm from the crestal bone to the occlusal plane, to allow for proper oral hygiene and sufficient thickness of the prosthetic material. Furthermore, they increase the lingual bulk of the prosthesis, which can encroach on tongue space. Finally, long-term maintenance is essential [24, 25].
CONCLUSION
The CAD/CAM implant overdenture bar with locator attachments is an effective treatment option for severely resorbed mandibular ridges. The custom-fabricated bar is precisely milled to create a flat horizontal surface that supports the denture, while the close adaptation of the denture base to the axial guiding planes provides enhanced lateral stability. Locator abutments offer reliable retention, and the drill-and-tap method used for attaching them ensures complete retrievability for maintenance. Processing the overdenture on a duplicate working cast facilitates easy prosthesis retrieval and preserves the master cast for future reference. Overall, the CAD/CAM implant overdenture bar with locator attachments is a practical solution to improve retention, support, and stability in complex cases.
AUTHORS’ CONTRIBUTIONS
The author confirms sole responsibility for the following: M.H.: Study conception and design, data collection, analysis and interpretation of results, and manuscript preparation.
ETHICAL STATEMENT
The clinical records, radiographs, and laboratory data were obtained directly from the patient during routine care at the School of Dentistry of Indiana University, in accordance with institutional ethical standards and with the patient's informed consent.
AVAILABILITY OF DATA AND MATERIALS
The data supporting the findings of the article will be available from the corresponding author [M.H] upon reasonable request.
ACKNOWLEDGEMENTS
The author would like to thank Dr. John A. Levon, Director of Advanced Education in Maxillofacial Prosthodontics and Dr. Orlando L. Cayetano, Clinical Assistant Professor of Prosthodontics, School of Dentistry, Indiana University, for their help and guidance to complete this case.