All published articles of this journal are available on ScienceDirect.
Fabrication of an Immediate Complete Denture with Digital Workflow: A Case Report
Abstract
Aim
Digital impression and CAD/CAM fabrication have had a profound impact on the field of dentistry, reducing patient discomfort and offering time-efficient solutions in numerous instances. The digital workflow can be described as a clinical and laboratory process that commences with the acquisition of a digital impression of the edentulous jaw, followed by a digital tooth setup and the fabrication of a complete denture using CAD/CAM techniques. The primary aim of this clinical case report is to highlight the potential that digital dentistry presents in the context of complete dentures.
Case Report
In the case presented, a fully digital workflow was employed to fabricate a complete maxillary denture for a patient with failing implant restorations. This fully digital approach eliminated the necessity to remove the existing implant restoration until the final appointment, reducing the chairside appointments to just two, in contrast to the five appointments typically required in a conventional approach.
Conclusion
This case report describes a fully digital method for creating an immediate maxillary complete denture without the need for prior tooth extraction, optimizing both time efficiency and cost-effectiveness. However, further research with larger sample sizes is necessary to confirm the digital technique's superiority over conventional methods.
1. INTRODUCTION
In the past decade, digital technology has introduced a more efficient workflow for complete dentures in dentistry than conventional methods [1]. The initial step in the process of digital complete dentures involves intraoral scanning of the edentulous arch or scanning the definitive impressions of the patient's cast, along with the digital recording of the existing occlusal relationship. Within the digital workflow, the design of the denture base and the arrangement of artificial teeth are accomplished, followed by the modeling of the denture using either an additive method (3D-printing) or a subtractive method (computerized numerical control milling) [2-4].
Errors in the digital workflow, especially in CAD-CAM, can be mitigated through direct intraoral scanning [5]. Other studies have suggested that mistakes or inaccuracies that previously occurred during the clinical and laboratory phases can now be prevented due to the improved accuracy of intraoral scanners [6].
The digital workflow offers substantial advantages for patients whose remaining teeth exhibit increased mobility. Intraoral scanning replaces the use of conventional impression materials such as irreversible hydrocolloids (alginate), polyethers, Polyvinyl Siloxane (PVS), vinyl siloxane ether (vinyl polyether siloxane), hydrophilic polyvinyl siloxane, fast-set elastomeric materials, and alginate substitute materials. All of these conventional materials possess stiffness and hardness that can lead to patient discomfort or even result in the extraction of a hopeless tooth during impression removal.
Following the completion of intraoral scanning, a digital model of the teeth and supporting soft tissues is created, and the images of the teeth are extracted from the virtual 3D cast [7], maintaining the digitally recorded vertical dimension. With conventional immediate dentures, assessing the Occlusal Vertical Dimension post-extraction is particularly challenging [8].
Previous studies have demonstrated that the digital workflow simplifies the laboratory process, reduces chair time, and minimizes the number of appointments [9, 10]. Additionally, it offers superior mechanical properties, the potential for digital archiving, and easy access to patients' digital files, favoring the digital procedure [1, 9, 11]. The digital workflow not only reduces the number of clinical appointments and chair time but also enhances the detection and visualization of the morphology of the edentulous arches and reduces the polymerization shrinkage of Polymethyl Methacrylate (PMMA) [12]. Furthermore, intraoral scanning is complemented by a mucostatic impression of the edentulous regions, which can be particularly helpful in cases of shallow and narrow alveolar ridges with limited depth or width.
Intraoral scanners can minimize patient discomfort, mitigate potential allergies to impression materials, and eliminate errors associated with the distortion of impression materials and changes in the cast. This also renders the storage of physical impressions and gypsum casts unnecessary [5].
2. CASE PRESENTATION
The initial treatment for this patient began 18 years ago, involving a treatment plan that incorporated 7 implants in the maxilla. These implants were promptly loaded with heat-cured acrylic provisional restorations (Fig. 1). While the patient was content with the provisional restoration, they did not proceed to complete the treatment with a definitive prosthesis. Over the years, the patient maintained this provisional restoration, even getting repairs done abroad, until presenting for treatment after 18 years (Figs. 2 and 3).
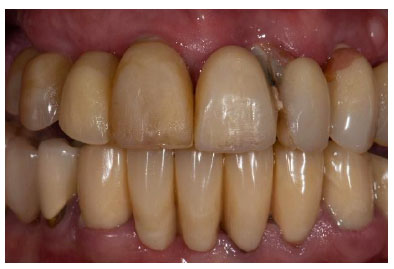
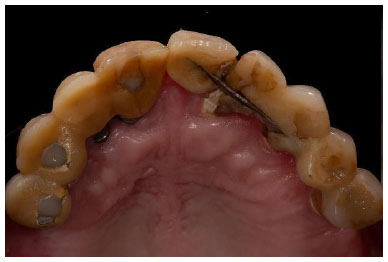
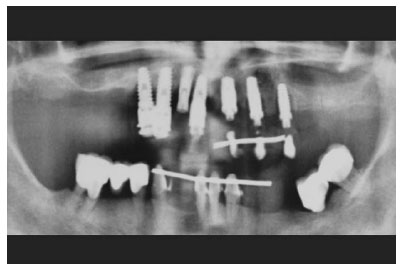
Upon clinical and radiographic examination, it became evident that the patient was dealing with generalized severe chronic periodontitis, peri-implantitis, and carious lesions on the mandibular teeth that were supporting the existing metal-ceramic restorations.
The treatment plan for this specific patient entailed the extraction of all existing implants in the maxilla and the fabrication of an immediate complete denture. Despite the severity of the clinical situation, the patient expressed a strong desire to avoid being edentulous, even for a brief period, and was insistent on retaining the existing restorations in the mandible.
Due to the increased mobility of the existing maxillary restorations, there was a heightened risk of their removal or fracture during the initial impression process. Consequently, a complete digital workflow was chosen for this patient. This workflow commenced with intraoral scanning using the TRIOS3 scanner by 3Shape A/S.
To capture digital impressions of the vestibular areas, the scan was performed with the lips and cheeks retracted using the scanner head while gently stretching the vestibular area with a retractor. Following the scanning of the maxillary arch, the opposing mandibular arch was also digitally scanned. The patient was requested to bite firmly, and the bite was recorded with the digital scanner on both sides. This process facilitated the completion of the occlusal registration, with the existing Occlusal Vertical Dimension duly recorded. Subsequently, the images of the scanned mandibular arch and opposing maxillary arch were meticulously aligned virtually, utilizing the virtual occlusal record as a point of reference (Figs. 4 and 5).
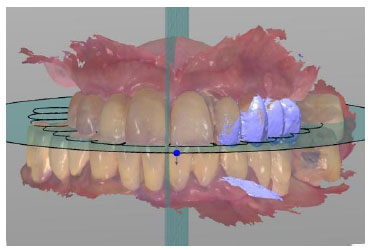
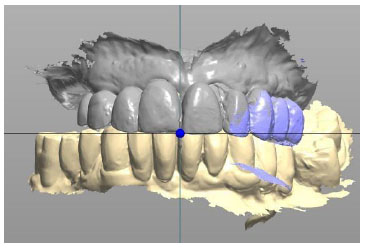
Once the virtual casts were acquired and mounted at the desired Occlusal Vertical Dimension (OVD), the images of the remaining teeth were selectively removed from the virtual 3D image of the maxilla (Figs. 6 and 7).
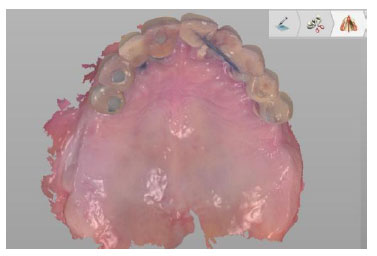
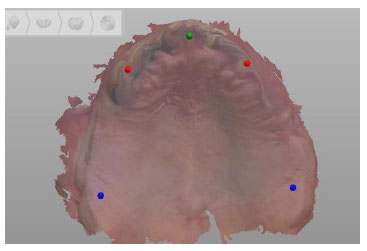
The gathered data were transferred into denture planning software (Dental System; 3Shape A/S, Denmark) for the digital design of the complete denture (Fig. 8). This program facilitated occlusal adjustment using a virtual articulator. It also enabled the creation of more precise denture teeth by simulating mastication with the virtual articulator.
Subsequently, the resulting data were exported to a 5-axis milling machine (Dentsply Sirona, inLab MC X5) for the denture fabrication process (Figs. 9 and 10). The denture base was milled from a Pink Polymethyl Methacrylate (PMMA) disk (IvoBase CAD Pink-V 98.5-30mm/1, Ivoclar Vivadent, USA). The denture teeth were also milled from PMMA disks (SR Vivodent CAD Multi BL3 98.5-20mm/1, Ivoclar Vivadent, USA) using the same milling device and fine milling tools. Following their separate fabrication, the milled teeth were securely affixed to the milled denture base sockets using a PMMA-based bonding material (Ivotion Bond Kit 10, Ivoclar Vivadent, USA).
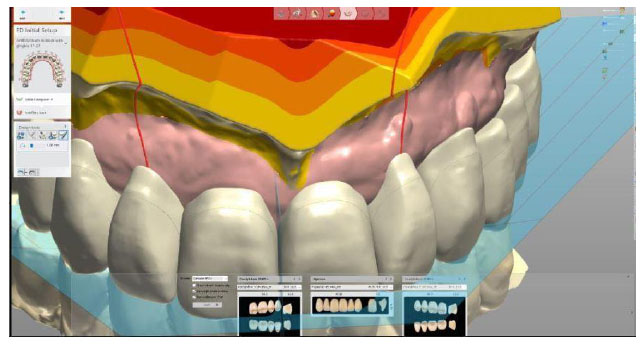
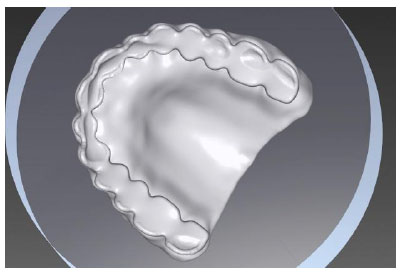
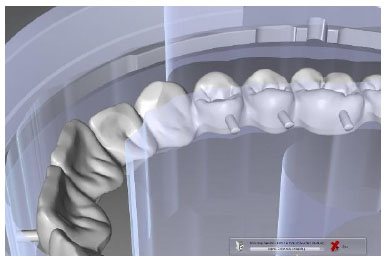
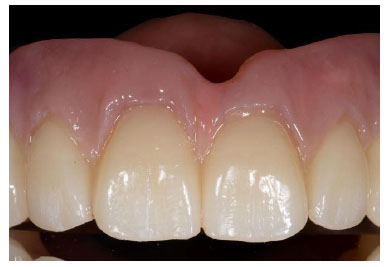
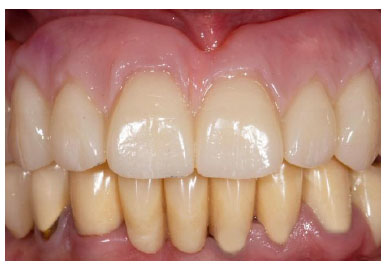
Regarding the time allocated for laboratory fabrication, it required six hours for the base, two and a half hours for the teeth, and just twenty minutes for the bonding process. Subsequent to the denture fabrication, the remaining implants were extracted in accordance with the treatment plan, and any excess bone and gingival tissues were carefully removed. Following this, the digitally fabricated maxillary immediate denture was inserted after suturing (Figs. 11 and 12). Only minimal chairside adjustments were required for the internal surface, borders, and undercut areas of the immediate denture, which had been lined with a soft tissue conditioning material (Coe-Comfort; GG America Inc). A week later, the sutures were removed, and the denture underwent a chair-side reline using a hard reline material following the removal of the tissue-conditioning material. The denture base exhibited excellent retention. The patient experienced no difficulty with mastication and expressed satisfaction with the esthetic outcome of the dentures.
Throughout the entire digital workflow for this case, there was no need to remove the existing implant restoration until the final appointment. This contrasts with the conventional protocol, where it would have been necessary to remove the old implant restoration for prosthetic rehabilitation at each appointment.
3. DISCUSSION
This case report presents a fully digital approach to fabricating immediate, complete dentures without the need for prior extraction or following a conventional workflow. The digital data were acquired through the utilization of an intraoral scanner, and the denture planning software, in conjunction with CAD-CAM technology, facilitated the denture fabrication within a fully digital workflow.
In the past, several techniques have been outlined for the fabrication of complete digital dentures, many of which still incorporate at least one conventional clinical step. In various case reports, researchers have suggested scanning existing casts, while others have advocated for the digitalization of conventional impressions [13-15]. In cases of this nature, some authors recommend an impression technique employing traditional impression materials such as irreversible hydrocolloids (alginate), polyethers, Polyvinyl Siloxanes (PVS), vinyl-siloxane ether (vinyl polyether siloxane), hydrophilic polyvinyl siloxane, fast-set elastomeric materials, or alginate substitute materials. This process is typically followed by the creation of a physical cast, which is then scanned.
For instance, in a 2020 case report [13], the maxillary and mandibular impressions were taken using silicone-based materials and alginate, respectively, and the gypsum casts were later digitized in the laboratory. Alternatively, some practitioners prefer the direct scanning of the impressions.
Furthermore, a case series [12] suggested that partial scans of the lower third and middle third of the face, or complete face scans, can be combined with intraoral scans to successfully generate a virtual model of the patient's face. This virtual model allows the clinician and technician to design the appropriate tooth shape and color, facilitating individual tooth arrangement during the denture design process.
In this case, these clinical steps were deemed unnecessary, given that the tooth's anatomical features concerning length, width, and overall shape were well preserved due to previous prosthetic restorations. Furthermore, the functional Vertical Dimension of the Occlusion of the patient had already been digitally recorded on the intraoral scanner before the extraction of the remaining implants and teeth.
It's worth noting that the conventional complete denture workflow has been the standard practice for the last seven decades and continues to be employed in routine clinical settings. Moreover, these conventional protocols for complete dentures typically entail multiple appointments. In the conventional approach, five appointments are required before the delivery of the denture, whereas in the digital workflow, only two sessions suffice.
Digital protocols facilitate the creation of immediate dentures without the necessity of using conventional impression materials or fabricating stone casts. These protocols prove to be especially advantageous in cases where teeth or implants with uncertain prognoses are slated for extraction and subsequent replacement with removable prosthetic rehabilitation, making immediate dentures the preferred choice. Furthermore, teeth exhibiting mobility or existing restorations can be safely extracted during the impression procedure.
In the digital workflow, the images of the teeth are efficiently digitally removed from the virtual arch, allowing dentists to design immediate dentures before the actual tooth extraction process. Given the time required for conventional steps like impressions, cast production, articulator mounting, and tooth removal from the cast, the digital workflow emerges as a time-saving and expedient approach.
Another noteworthy clinical advantage of the digital workflow is the ability to archive the acquired digital impressions and fabrication data, providing the option to manufacture a replacement or duplicate denture whenever necessary.
In a clinical study conducted by AlHelal et al. [16], the retention achieved from the milled bases, constructed using polymethylmethacrylate resin, was substantially greater than that of conventionally heat-cured denture bases. This substantial improvement in retention, coupled with the lack of notable changes in tooth position or deformations in denture bases, results in the achievement of a bilateral balanced occlusal concept.
While digital scanning has indeed demonstrated time-saving and significant clinical advantages, as previously mentioned, in comparison to conventional impression techniques, it's essential to acknowledge that challenges persist, particularly regarding mobile soft tissues in the vestibular area. In cases involving maxillary dentures, the utilization of a scan retractor can be invaluable for digital impressions, as it aids in the retraction of mobile tissues and the gentle stretching of the vestibular area [17].
Certain authors have raised concerns regarding intraoral scanning for complete dentures, particularly in cases where a patient's lips and cheeks exhibit considerable tightness. Scanning immobile tissues such as the hard palate or alveolar ridges is generally less challenging compared to scanning the mobile tissues in the vestibule, which significantly contributes to the retention of complete dentures.
Furthermore, in some instances, imprecise scanning of the vestibule can result in an inadequate border seal. In such cases, it becomes imperative to perform a relining of the base of the complete denture to ensure proper fit and retention [16].
The utilization of digital technology in the fabrication of complete dentures can be effectively integrated with conventional techniques. For instance, in a clinical trial involving 40 patients, it was found that complete dentures produced through 3D printing exhibited comparable accuracy and patient satisfaction levels when compared to conventional methods [18]. Furthermore, in situations where denture duplication was required, the digital technique demonstrated superior accuracy in comparison to the conventional approach [19].
The effectiveness of CAD/CAM dentures has previously been documented in a case series involving 15 patients and implementing a two-visit protocol [20]. A systematic review published in 2021 [21] assessed 14 in vitro articles and reached the conclusion that digital complete dentures exhibited similar or even superior adaptation when compared to conventional complete dentures. Notably, the posterior palatal seal and border seal areas were identified as the primary challenges in the context of digital complete dentures. Additionally, the review found that denture accuracy couldn't be effectively compared between CAD-CAM milling and 3D printing.
The clinical effectiveness of digital technology in the production of complete dentures has been further affirmed in a single-blinded clinical study [22], which demonstrated improved stability in digitally fabricated dentures. However, in the same study, it was noted that conventionally fabricated dentures excelled in terms of polishing.
In a systematic review based on 18 papers [23], the clinical advantages of dentures crafted with CAD/CAM techniques were thoroughly investigated. This review highlighted that patient acceptance significantly increased due to superior fit, reduced chair time, shorter appointments, and fewer post-insertion visits.
Moreover, clinical case reports [24] and reviews [25] focusing on digitally fabricated dentures completed in just two appointments highlight the effectiveness of this treatment option.
The current case report delineates a fully digital approach for constructing an immediate maxillary complete denture, eliminating the requirement for tooth extraction and subsequent healing time prior to impression taking. Intraoral scanning of the maxilla is a straightforward process, distinct from the challenges encountered when scanning mobile tissues like the vestibular areas, where scan retractors become necessary. Although the digital workflow employed in this particular complete denture case was both time-efficient and cost-effective, additional studies involving larger sample sizes are imperative to establish the superiority of the digital technique in comparison to conventional methods.
CONCLUSION
The utilization of digital impression and CAD/CAM fabrication in the realm of dentistry has ushered in a transformative era, significantly enhancing patient comfort and streamlining treatment processes. This case report underscores the remarkable potential of digital dentistry in the creation of complete dentures, as demonstrated by the successful fabrication of a complete maxillary denture for a patient with failing implant restorations. By employing a fully digital workflow, we achieved remarkable time efficiency and cost-effectiveness, reducing chairside appointments and eliminating the need for prior tooth extraction. While our findings are promising, larger-scale studies are warranted to definitively establish the superiority of digital techniques over conventional methods. Nonetheless, this report contributes valuable insights into the promising future of digital dentistry, paving the way for enhanced patient care and treatment outcomes in prosthodontics.
AUTHORS' CONTRIBUTIONS
It is hereby acknowledged that all authors have accepted responsibility for the manuscript's content and consented to itssubmission. They have meticulously reviewed all results and unanimously approved the final version of the manuscript.
LIST OF ABBREVIATIONS
PVS | = Polyvinyl Siloxanes |
PMMA | = Polymethyl Methacrylate |
ETHICAL STATEMENT
The treatment of the patient that is described in the above mentioned case report was carried out in a private practice. For this reason, there was no need for approval from the Ethical Committee of our University.